Lithium is the lightest metal on the periodic table and has exceptional properties making it an invaluable ingredient in diversified manufacturing applications. It is widely used in batteries, ceramics, glass, lubricants, grease, pharmaceuticals, rubber, optical and air-conditioning industries, etc. Because of that, lithium recovery has become one of the most important processes.
It plays a crucial role in the transition to clean energy for mitigating the adverse effects of climate change.
Pegmatites constitute the second major economic resource of lithium after brines, accounting for about 25 % of global production. Minerals hosted by pegmatite rocks include spodumene, lepidolite, petalite, amblygonite, zinnwaldite, triphylite, and eucryptite. Spodumene is the principally mined lithium-bearing mineral due to its high theoretical lithium content of about 8.1 % Li2O.
Lithium-bearing minerals are tough to process. Lithium recovery from spodumene generally involves a combination of physical, thermal, and chemical treatment techniques. The major drawback is usually associated with spodumene’s physical and chemical properties and its associated gangue impurities.
1. Beneficiation techniques
The literature reports the application of different processing techniques to separate spodumene from its associated gangue impurities. The finely liberated spodumene-bearing ores are processed following flotation, magnetic separation methods, and dense media separation (DMS). DMS is applied for ores having coarser liberation sizes.
Flotation
The most widely accepted and proven practice of beneficiating lithium-bearing spodumene is flotation. It’s a physicochemical technique of separating spodumene from associated gangue impurities by exploiting the difference in their surface properties. It is an effective technique for treating fine particles with a very nominal difference in specific gravity between the valuables and rejects, which cannot be recovered using gravity concentration techniques.
Its superior performance leads to the generation of high-grade concentrates and is a valid replacement for the DMS technique (Dense media separation). Still, the flotation technique poses a serious challenge because of its comparable surface properties and isoelectric point to its associated gangue impurities, such as quartz and feldspar.
The most widely used anionic collectors for spodumene flotation from pegmatites include oleic acid, sodium oleate, and sulfonated and phosphorated fatty acids. Flotation studies conducted at a pilot scale on the pegmatite of Cleveland County (USA), using oleic acid, resulted in a recovery of 76.7 % spodumene, having a grade of 6.4 % Li2O. The de-slimed material of Kings Mountain pegmatites in North Carolina, USA, when floated with tall oil fatty acid in the presence of a glycol-type frother, yielded a spodumene concentrate having an assay of 6.34 % Li2O and 93.5 % recovery.
The amblygonite free gravity concentrate of the Bernic Lake pegmatite processing plant in Canada is floated with a mixture of petroleum sulfonate and fatty acids as the collector to produce a spodumene concentrate assaying 7.25 % Li2O.
The latest research is inclined towards exploiting the effects of using a combination of anionic/cationic collectors. Their significant collective influence over single collectors is shown in Table 1.
Table 1. Summary of the research on spodumene collectors.
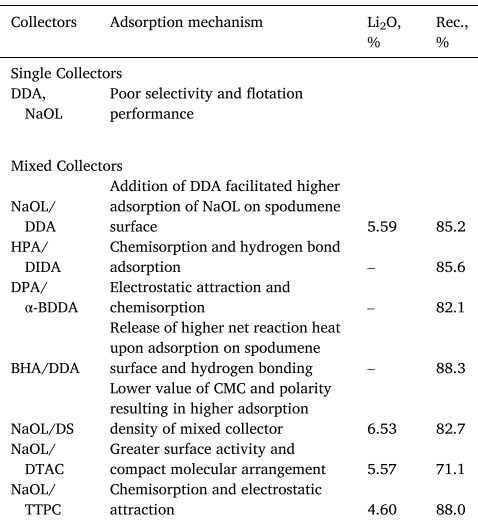
Magnetic separation
The scattered presence of magnetic minerals within the spodumene crystal lattice poses a challenging task for their efficient separation from spodumene using gravity or flotation techniques. The most common magnetic minerals associated with the pegmatites include tourmaline and amphibole. The maximum allowable content of iron oxide in the glass or ceramic-grade spodumene concentrate should not exceed 0.5 %.
Magnetic separation is used, before or after flotation, to remove the iron-bearing gangue impurities associated with spodumene. The partially purified spodumene concentrate is fed to the flotation cells for the recovery of amblygonite, quartz, and Na-feldspar. Finally, the flotation concentrate is treated in a wet high-intensity magnetic separator to remove the magnetic impurities and produce a spodumene concentrate assaying 7.25 % Li2O.
2. Pyro-metallurgical techniques for lithium recovery
The beneficiation process generally follows a combination of pretreatment and extraction techniques to recover lithium from the beneficiated concentrate in the marketable form. Pre-treatment induces higher reactivity to the monoclinic crystal-shaped α-spodumene. It can be done by facilitating its transformation into tetragonal structured β-spodumene at elevated temperatures. The third phase, commonly known as γ-spodumene, having a hexagonal structure, is reported to occur during the transition of α– to β-spodumene.
However, γ-spodumene being metastable in nature transforms into β-spodumene at higher temperatures. This phase transformation process from α– to γ-spodumene is reported to occur in the temperature range of 700–900 °C. γ-spodumene transforms into β-spodumene between 900 and 950 °C, beyond which spodumene fuses. Higher temperature increases the porosity of the ore on account of its volumetric expansion. It also reduces the density and hence creates a greater exposed surface area for acid attack during the leaching process. However, roasting is the most prevalent pre-treatment technique. It involves the addition of a suitable additive or a reagent to facilitate the generation of soluble lithium salt complexes. Some of them are LiCl, Li2SO4, LiOH, and Li2CO3, which can be further recovered using leaching.
Sulfation
Sulfation relies on the formation of highly stable, water-soluble lithium sulfate complexes by the addition of alkali metal sulfates, sulfuric acid, and SO3 gas during the heating process. The close association of Li with other metallic impurities, such as Na, Mg, Al, K, and Fe, leads to the formation of other soluble sulfates in addition to lithium sulfate and thereby reduces the overall recovery of lithium. A recovery of about 99.7% lithium has been reported in the sulfation roasting of β-spodumene using SO3 gas at a temperature range of 225–425 °C. The reactions of the leaching and precipitation are shown below.
2 LiAlSi2O6 + H2SO4 → Li2SO4 + 4 SiO2 + Al2O3 + H2O
Li2SO4 + Na2CO3 → Li2CO3↓ + Na2SO4
Literature reports roasting of spodumene with concentrated sulfuric acid at 250 °C to produce a water-soluble lithium sulfate. Then it can be further precipitated in the presence of sodium carbonate to recover lithium in the form of lithium carbonate. The influence of impurities was determined on lithium extraction using 30 % excess sulfuric acid rather than the stoichiometric requirement. The results showed a lithium extraction efficiency of 97.1 % under optimized conditions, close to the maximum attainable value of 98 %. The impurities did not limit lithium recovery using an acid consumption mechanism. Instead, they prevented the complete digestion process by physically obstructing β-spodumene particles, thereby restricting the maximum extraction to 98 %.
Carbonation
This process utilizes the addition of alkali carbonates during the heating of the spodumene ore to form soluble lithium complexes, which can be readily leached out. Several authors have reported the successful application of carbonates of sodium and calcium for efficient lithium recovery. The roasted product is generally water-leached to yield lithium carbonate. The lithium carbonate can be further precipitated with carbon dioxide gas to form more soluble lithium bicarbonate. Lithium extraction efficiency increases upon leaching with HCl or H2SO4. These are the reactions of the carbonation process.
2 LiAlSi2O6 + Na2CO3 → Li2CO3 + Na2O.Al2O3.4SiO2.H2O
Li2CO3 + CO2 + H2O → 2 [LiHCO3]↓
This process is much more economical and safer as it does not involve the consumption and usage of concentrated acids. However, it suffers a significant drawback of the high consumption of energy involved in the decrepitation of alkali carbonate additives.
Chlorination
The chlorination process employs the application of various chlorinating agents. Most frequently used are chlorine gases or chloride-based salts for lithium recovery. The soluble lithium chloride, thus formed, is water-leached and further precipitated to recover lithium carbonate. The chlorination reactions can be summarized as follows:
LiAlSi2O6 + 1/2 Cl2→ LiCl + 1/6 Al6Si2O13 + 1/4 O2
LiCl + Na2CO3 → Li2CO3↓ + NaCl
However, this technique has failed to draw much attention from researchers. The main drawbacks are the toxicity of the chlorine gas and the need for expensive corrosion-resistant equipment. Despite the above shortcomings, this process offers significant advantages. For example higher selectivity in the removal of the impurities associated with spodumene, thereby resulting in increased recoveries.
3. Hydro-metallurgical techniques for lithium recovery
Acid digestion
Hydrofluoric acid has been used to leach β-spodumene to form lithium fluoride. The by-products of the reaction are utilized to produce fluxing reagents for the extraction of aluminum. The extraction efficiency relies on the optimum temperature, time, acid concentration, and feed particle size. A mixture of hydrofluoric and sulfuric acids has been reported to dissolve α-spodumene and extract 96 % lithium at a temperature of 100 °C, following an ion-exchange mechanism. Given the perilous effect of the direct addition of hydrofluoric acid into the leaching system, the SiLeach process was developed. In this process, a mixture of fluoride salt (CaF2) and sulfuric acid was used to dissolve α-spodumene.
This process is much more economical and energy efficient as it evades the requirement of high-temperature decrepitation of α– to β-spodumene. A mixture of β-spodumene and nitric acid, heated at a temperature of 170 °C under pressurized conditions for an hour, resulted in the production of lithium nitrate. The lithium recovery was reported to be about 95 % under optimized conditions. The recovery decreased at lower temperatures and pressure.
Alkali metal salt digestion
Calcium hydroxide was used to dissolve the insoluble silicates and increase the recovery rate. Similar to acid leaching, the leaching rate was controlled by temperature, time, and feed particle size. The important parameter is also the concentration of metal salt. Similarly, attempts have been made to use sodium carbonate as a potential lixiviant for lithium recovery. It proved to be more efficient under a pressurized atmosphere. The influence of leaching temperature, time, the concentration of lixiviant, feed particle size, and agitation speed on the lithium extraction efficiency was thoroughly investigated. The application of sodium sulfate solution in conjunction with lime has proved to be a potential lixiviant for extracting lithium from spodumene. With this method, about 90 % of lithium can be recovered when subjected to leaching at 230 °C for 3 h.
Alkaline digestion
The literature reports the application of various alkali reagents, such as lime, sodium, or potassium hydroxide, for the digestion of spodumene to extract lithium. The application of alkaline digestion in lithium extraction from α-spodumene was also investigated. Figure 1 shows the SEM images of the α-spodumene ore and leach residue obtained under optimized conditions. Obviously from the figure the morphology of spodumene altered significantly from an irregular to a regular wedged shape with a smooth surface and good crystallinity after leaching with calcium oxide and sodium hydroxide. However, most of these processes could yield a leaching efficiency of close to 90% only. A higher extraction efficiency of about 99% was achieved using caustic soda as the lixiviant under optimized conditions.
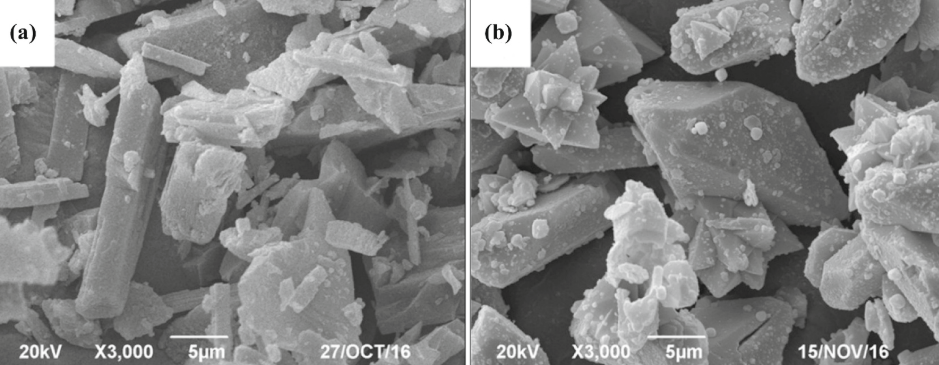
Figure 1. SEM images of α-spodumene ore (a) and leach residue (b) under optimized leaching conditions with CaO and NaOH.
Bio-leaching
The beneficiation, as well as the extraction processes discussed above, are energy-intensive techniques. Further to this, spodumene is very unstable in natural atmospheric conditions. In such a perspective, the role of microorganisms becomes crucial in developing a less energy-intensive and eco-friendly economic process for lithium recovery from spodumene. The micrographs reveal the fungal growths upon attack of the spodumene surface by P. purpurogenum and R. rubra. However, no spores or vegetative filaments could be observed on the spodumene surface attacked by A. niger.
The attack mechanism of A. niger and P. purpurogenum was facilitated by soluble low-weight molecular metabolites. However, R. rubra, attacked the mineral by its metabolic activity, which required physical contact to leach the metals out of it. However, it is to be noted that the bioleaching technique suffers from a significant drawback. Slow reaction kinetics and very low extraction efficiency are still major challenges. Hence, it requires extensive research on spodumene’s bioleaching to assess the possibility of its acceptance on an industrial scale.
4. Conclusion
The major problem of primary sources of lithium (brines) is their limited geological occurrences. These geological limitations make it hard to exploit for some countries that don’t have these findings. Therefore, pegmatites are emerging as a chief source of lithium due to their accessibility and ability to meet the lithium demand. Among the hard rock resources, spodumene is the principal source of lithium. The reason for this is the highest content.
All of these mentioned methods serve their purpose for lithium recovery, but most of them have major drawbacks such as ecological impact. Aiming for the zero-waste principles and circular economy would add a high value to the processes and fight the global changes on the planetary scale. So far excessive studies have been conducted to prevent waste generation in this process. The main process for lithium recovery is a sulfuric acid method that generates high amounts of hardly commercialized sulfuric salts. Nevertheless, the typical flowsheet of lithium recovery from spodumene is shown in Figure 2.
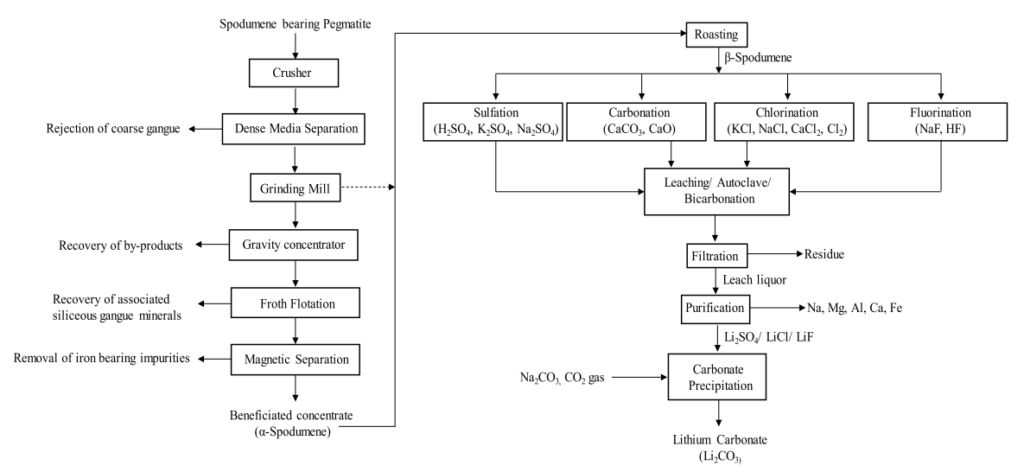
Figure 2. A typical flowsheet illustrating the recovery of lithium from spodumene.
The source:
Kundu, et. al, Recovery of lithium from spodumene-bearing pegmatites: A comprehensive review on geological reserves, beneficiation, and extraction
DOI: /10.1016/j.powtec.2022.118142